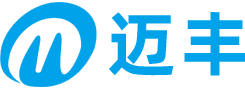
生产PVC发泡板时出现泡空(或称泡孔)的问题,通常是由多种因素共同作用导致的。以下是对该问题的详细分析:
发泡剂过量:发泡剂是PVC发泡过程中产生泡孔的关键原料,但过量使用会导致泡孔过大或数量过多,从而影响板材的整体质量。
发泡调节剂不足或质量问题:发泡调节剂用于控制发泡过程,如果其用量不足或质量不佳,会导致发泡不稳定,进而产生泡空现象。
塑化不良:PVC树脂在加工过程中需要充分塑化,如果塑化不良,会导致熔体强度不足,无法支撑发泡过程中产生的泡孔,从而形成泡空。
加工温度低:加工温度是影响PVC塑化和发泡的重要因素。如果加工温度过低,PVC树脂无法充分塑化,发泡效果也会受到影响,容易产生泡空。
润滑过量:适量的润滑剂有助于PVC树脂的流动和加工,但过量使用润滑剂会导致熔体粘度降低,泡孔容易合并或破裂,形成泡空。
模具设计不合理:模具的结构和温度分布对发泡过程有很大影响。如果模具设计不合理,如流道不畅、冷却不均等,都会导致发泡过程中泡孔分布不均或产生泡空。
挤出机性能:挤出机的性能直接影响到PVC发泡板的挤出效果。如果挤出机性能不稳定或存在故障,如螺杆磨损、温控不准等,都会导致发泡过程中产生泡空。
模具磨损:模具在使用过程中会逐渐磨损,导致流道变宽或变窄,从而影响发泡过程中泡孔的形成和分布。磨损严重的模具更容易产生泡空现象。
操作不当:如加料速度不均匀、牵引速度不稳定等,都会对发泡过程产生影响,导致泡孔分布不均或产生泡空。
混料不均:混合原料时未按规定的程序、温度和时间进行操作,导致原料混合不均匀,也会影响发泡效果并产生泡空。
调整发泡剂和发泡调节剂的用量:根据发泡效果调整发泡剂和发泡调节剂的用量,确保二者比例协调且用量适中。
提高加工温度:在合理范围内提高加工温度,确保PVC树脂充分塑化。
减少润滑剂用量:适当减少润滑剂的用量,以提高熔体粘度并改善发泡效果。
优化模具设计:改进模具的结构和温度分布设计,确保发泡过程中泡孔分布均匀且不易产生泡空。
加强设备维护和检修:定期对挤出机和模具进行维护和检修工作,确保其性能稳定并减少故障发生。
规范操作流程:加强操作人员的培训和管理工作,确保操作过程规范且稳定可靠。