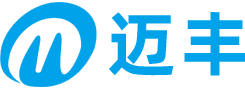
PVC共挤发泡板的生产工艺流程是一个复杂且精细的过程,主要包括以下几个关键步骤:
原料选择:主要原料为聚氯乙烯(PVC)树脂,同时需要准备各种辅助材料,如发泡剂、稳定剂、填充剂、润滑剂以及可能的增强剂或色母粒等。这些材料的选择需根据产品要求和生产配方进行。
原料配比:根据生产订单和配方要求,精确计算并配比各种原材料和辅助材料的比例。配方的比例往往因生产设备、原辅料来源及生产要求的不同而有所差异。
热混:将PVC树脂和各种辅料称量后放入热混锅中,通过加热和搅拌使各种原料充分混合均匀。这一步骤有助于提高原料的塑化效果和后续加工性能。
冷混:经过热混后的物料自动进入冷混锅中进行搅拌冷却。冷混的目的是降低物料的温度,防止过热分解,并进一步提高混合均匀度。
挤出成型:将混合均匀的原料通过挤出机进行挤出。挤出机的高温高压环境使原料熔化为黏流态,并通过模具赋予板材初始形状。
发泡处理:在挤出机出口处对PVC板材进行发泡处理。发泡剂在高温下分解产生气体,使PVC板材发生膨胀和膨化,形成多孔的发泡结构。发泡过程对板材的质量和性能有决定性影响,需要严格控制发泡速度和均匀性。
快速冷却:发泡处理后的PVC板材通过冷却辊进行快速冷却,以固化发泡结构并确保板材的稳定性和平整度。
定型处理:冷却后的板材进入定型模具进行进一步定型处理,以确保板材的尺寸精度和形状稳定性。
压花与切割:根据需要,可以对板材进行压花处理以增加表面纹理和装饰效果。随后通过切割设备将板材切割成所需的长度和宽度。
检验与包装:对切割后的板材进行质量检验,确保符合生产标准和客户要求。合格的板材进行包装和堆放,以便后续运输和使用。
在PVC发泡板的生产过程中,还可以采用共挤技术来提高板材的性能或增加特殊功能。共挤是指将两种或多种不同性能的塑料同时挤出并复合在一起的过程。通过共挤技术,可以在PVC发泡板表面形成一层或多层具有特殊性能的薄膜层(如耐磨层、抗紫外线层等),从而提高板材的整体性能和使用寿命。
综上所述,PVC共挤发泡板的生产工艺流程是一个多步骤、多环节的复杂过程,需要严格控制各个环节的工艺参数和操作条件以确保产品质量和性能的稳定性和可靠性。