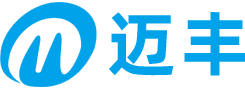
PVC发泡板一边薄一边厚的原因可以归结为以下几个方面:
模唇缝隙设置不合理:
模唇缝隙的大小直接影响挤出材料的厚度。如果模唇缝隙设置不一致,一侧较宽而另一侧较窄,就会导致挤出的材料一侧厚而另一侧薄。
阻流块调节不当:
阻流块用于调节挤出材料的流量。如果阻流块调节不当,使得一侧的流量大于另一侧,就会导致发泡板一侧厚度增加。
模具温度设置不合理:
模具温度的设置对挤出材料的流动性和冷却速度有重要影响。如果模具温度设置不当,一侧温度过高或过低,都可能影响材料的冷却和固化过程,从而导致厚度不均。
内外润滑不均衡:
在PVC发泡板的生产过程中,内外润滑剂的平衡对板材的厚度控制至关重要。如果内润滑剂过多,可能导致板材中间部分厚度增加;而外润滑剂过多,则可能使板材两侧走料过快,造成边缘部分较薄。
挤出机螺杆转速不稳定:
挤出机的螺杆转速直接影响材料的挤出速度和压力。如果螺杆转速不稳定,可能导致挤出速度时快时慢,进而影响发泡板的厚度均匀性。
口模磨损或设计不合理:
口模的磨损或设计不合理也可能导致发泡板厚度不均。例如,口模内壁不平整或存在磨损,会使得材料在挤出过程中受到不均匀的阻力,从而影响板材的厚度。
配方调整不当:
PVC发泡板的配方中包含多种原料和添加剂。如果配方调整不当,如内外润滑剂的配比不合适,也会影响板材的厚度均匀性。
原料质量波动:
原料的质量稳定性对发泡板的厚度也有一定影响。如果原料质量波动较大,如分子量分布不均或杂质含量高等,都可能导致发泡板厚度不均。
针对以上原因,可以采取以下措施来解决PVC发泡板一边薄一边厚的问题:
调整模唇缝隙和阻流块:
根据生产情况调整模唇缝隙和阻流块的位置和大小,确保挤出材料的流量和厚度均匀。
优化模具温度设置:
检查并调整模具温度设置,确保两侧温度一致且适合材料的冷却和固化过程。
调整润滑剂配比:
根据生产实际情况调整内外润滑剂的配比,确保板材厚度均匀且表面质量良好。
维护和更换设备:
定期检查和维护挤出机、口模等设备,及时更换磨损或损坏的部件,确保设备处于良好的工作状态。
稳定原料质量:
严格控制原料质量,选择质量稳定、可靠的供应商,减少原料质量波动对发泡板厚度的影响。